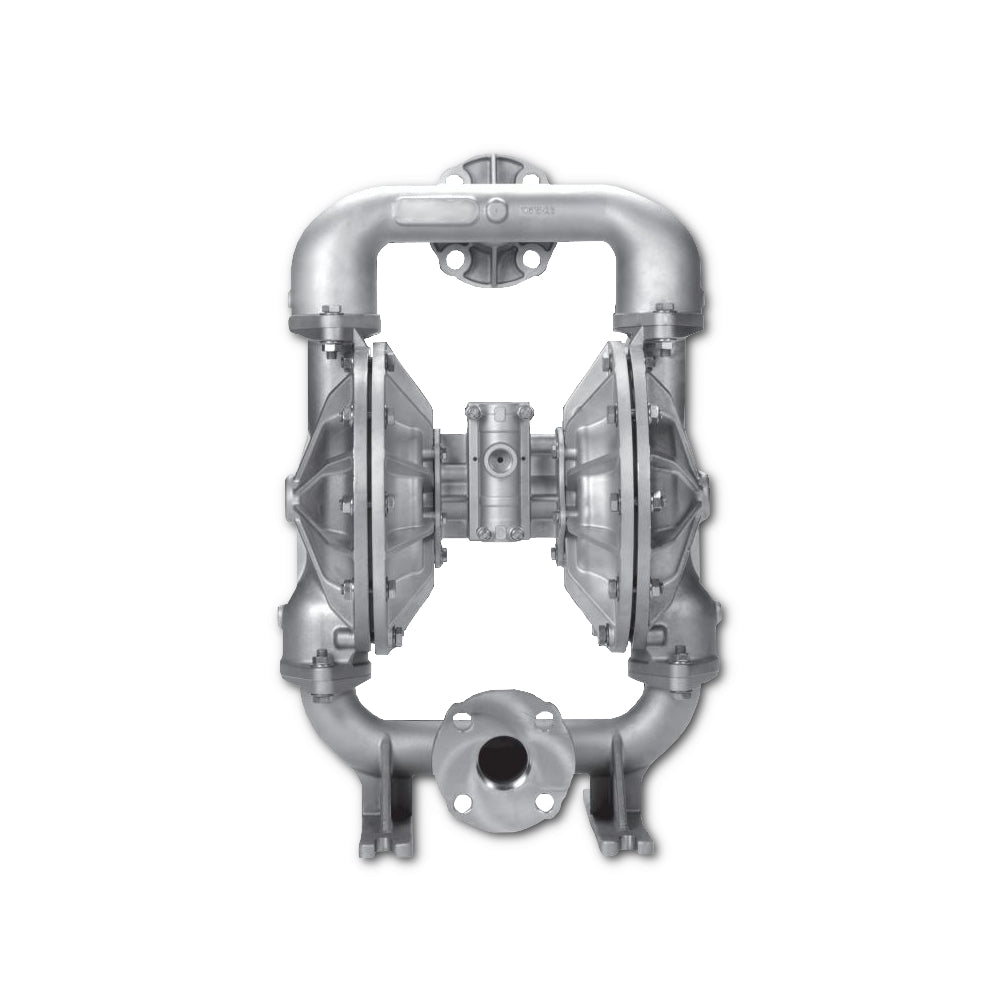
Aluminium Body Industrial Diaphragm Pumps
Freight costs for heavy & bulky items includes a tailgate truck cost. If a forklift is available please contact our sales team to discuss.
You can also contact us for a freight quote prior to ordering.
For orders outside of Australia contact us for a quote.
Scintex can ship worldwide.
Description
Made in the USA this aluminium body double diaphragm pump with Geolast diaphragms, valve balls, polypropylene valve seats and buna-n o-rings and seals, with standard suction configuration (suction centre front/discharge centre rear). Rubber diaphragms and seals, which allows it to be used with a range of fluids. It is reliable and simple to use and is great for transferring motor oil, vegetable oils and diesel which makes it ideal for mechanical and farming operations.
Air Driven Diaphragm Pump with Aluminium Body
Diaphragm pumps air-valve directs pressurized air behind the diaphragm on the right, causing the diaphragm on the right to move outward (to the right). Since both right diaphragm and the left diaphragm are connected via a diaphragm rod, when the right diaphragm moves to the right, the left diaphragm (through the action of the diaphragm rod) moves to the right also.
When the diaphragm on the left side is moving to the right, it is referred to as suction stroke. When the left diaphragm is in its suction stroke, the left suction ball moves upward (opens) and the left discharge ball moves downward (closes). This action creates suction and draws liquid into the left side chamber.
The air-valve directs pressurized air behind the left diaphragm, causing the left diaphragm to move outward (to the left). Since both the left diaphragm and the right diaphragm are connected via a diaphragm rod, when the left diaphragm moves to the left, the right diaphragm (through the action of the diaphragm rod) moves to the left also. When the diaphragm on the left side moves outward, the left discharge ball moves upward (opens) and the left suction ball moves downward (closes). This causes the liquid to leave the left side liquid outlet of the pump. Simultaneously, the right diaphragm moves inward (to the left), which causes the right suction ball to open and the right discharge to close, which in turn causes suction, drawing liquid into the right chamber. The process of alternating right suction / left discharge (and vice-versa) continues as long as compressed air is supplied to the pump.
Note, whilst this pump may be chemically compatible with petrol, it is not certified for use with petrol and therefore we can not recommend if for this use.
Pump Features
- 435LPM and 719LPM pump sizes available
- Common air supply connection type
- 1:1 Pressure Ratio
- High suction lift capabilities
- Self-priming
- Includes grounding capability to eliminate static discharge
- Rugged Aluminium pump body
- Anti-freeze/anti-stall
- Bolted construction ensures simple maintenance
- Externally serviceable air distribution systems
Chemical Pump Application
- Flammable Liquid Transfer
- Drum Decanting
- General Transfer
- Oils and Hydrocarbons
- Acids and Chemicals
Mining Pump Application
- General Transfer
- Water & Dewatering
- Tanker Unloading
- Drum & Container Transfer
- Acids and Chemicals
- Oils and Hydrocarbons
Paint, Printing & Packaging Pump Application
- General Transfer
- Ink
- Dosing
- Drum & Container Transfer
Food & Beverage Pump Application
- Sanitary
- General Transfer
- Pastes, Creams & Sauces
- Drum & Container Transfer
Always check the chemical compatibility of the fluid your pumping against the wet materials of construction before purchasing a pump.
Operation
The Air-Operated Double Diaphragm Pump requires a minimum of 20 psi of air to operate, with some variation according to diaphragm material. Increasing the air pressure results in more rapid cycling of the pump and thus a higher liquid flow rate. In order to not exceed 120 psi of inlet air pressure, and for accurate control of the pump, it is suggested to use a pressure regulator on the air inlet.
An alternate means of controlling the flow rate of the pump is to use an inlet air valve and partially open or close accordingly. When the air valve is completely in the closed position, the pump will cease to operate.
SDPA150- 435LPM (1-1/2" Rubber) Pump Version Data
SDPA200- 719LPM (2" Rubber) Pump Version Data
All-Flo Pump Specifications
Model | A150 | A200 |
---|---|---|
Liquid Port Size | 1-1/2" | 2" |
Liquid Connection Types | Female BSP | Female BSP |
Standard Suction Port | Center Front | Center Front |
Standard Discharge Port | Center Rear | Center Rear |
Air Inlet Connection Size |
3/4". FBSP |
3/4". FBSP |
Size | 284mm (L) x 528mm (W) x 439mm (H) | 343mm (L) x 498mm (W) x 668mm (H) |
Weight | 20 kg | 28 kg |
Performance | A150 | A200 |
---|---|---|
Max Flow | 435 lpm | 719 lpm |
Max Air Pressure | 120 psi (8.2 bar) | 120 psi (8.2 bar) |
Max Static Suction Head | 7.0 m-H2O | 7.0 m-H2O |
Max Suction Lift (Dry) | 6.4 m-H2O | 7.4 m-H2O |
Max Suction Lift (Wet) | 9.4 m-H2O | 9.7 m-H2O |
Max Solids | 1/4". (6.4mm) | 1/4". (6.4mm) |
Avg. Displacement Per Stroke | (0.30 G / 1.15 l) | (0.62 G / 2.34 l) |
Sound Level | 80 dBa (with Muffler) | 80 dBA (with Muffler) |
Construction | A150 | A200 |
---|---|---|
Wet End | Aluminium, Anodized Aluminium | Aluminium, Anodized Aluminium |
Air End | Aluminium | Aluminium |
Diaphragm | Geolast®, PTFE, Santoprene® | Geolast®, PTFE, Santoprene® |
Valve/Balls | Geolast® (Approximately same chemical compatibility as Buna), PTFE, Santoprene® | Geolast® (Approximately same chemical as Buna), PTFE, Santoprene® |
Seats | Aluminium, Polypropylene, Stainless Steel | Stainless Steel, Aluminium, Nylon, Polypropylene |
O-Rings | Buna-N, EPDM, PTFE | Buna-N, EPDM, PTFE, Viton® / FKM |
Hardware | Plated Steel, Stainless Steel | Plated Steel, Stainless Steel |
Muffler | Metal, Plastic | Metal, Plastic |